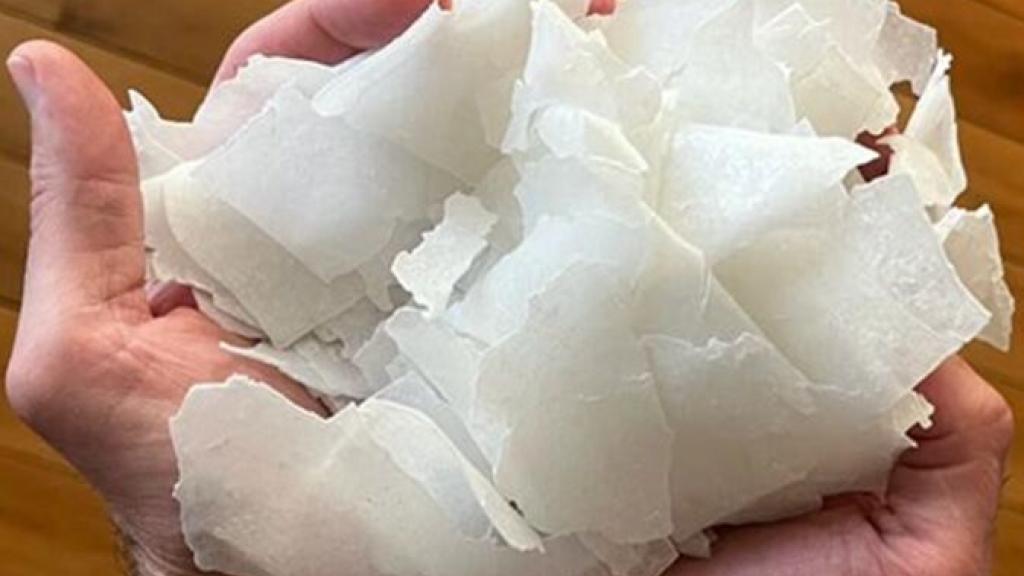
The PVB material used in glass lamination in form of a thin film was developed in the late 1930s. Its major raw material components are manufactured by the petrochemical processing of oil and gas, which clearly indicates a high CO2 load. AGC's commitment to carbon neutrality focuses not only on direct emissions from consuming fossil energies in our furnaces but also on indirect emissions such as the ones from the raw materials needed for our operations. With 141k tons, virgin PVB is the second most CO2 intensive raw material after soda ash, and there are ways to reverse the trend. The CO2 footprint of recycled PVB is 90% lower.
Tests to develop bio-based PVB never led to satisfying results so it became obvious that recycling was the only way to go. In itself, the recycling process is quite easy and recycled PVB was introduced to the market more than 30 years ago. In fact, ACG Czech was the first customer and pioneer user of recycled PVB from Czechtrim, who in the 80s developed the original technology of recycling the PVB trimmings into PVB film. Today, the recycled PVB is produced by Kuraray Europe in Czech Republic.
But there are challenges to overcome. Only clear (no acoustic or colored) PVB trimmings can be utilized to produce recycled PVB and the trimming waste volume represents 15% of purchased PVB volume at best. The second challenge for the coming years is to succeed in recycling PVB from scrapped laminated glass.
AGC Europe and AGC Automotive Japan are working on a process to recover PVB material from scrapped laminated glass from their automotive and architectural production lines. There is still a long way to go until the cleaning process of separated PVB is defined and the material flow is set, but the first results show that we are on the right track to succeed.